一、团队介绍
团队依托工业结构装备分析国家重点实验室、车辆工程国家级虚拟仿真教学中心,始终秉承“求实创新”的科研精神,并深度融入国家和地方发展战略需求,多年来致力汽车产业链的各个技术领域的研究,在汽车先进设计与制造、新能源动力系统与整车驾驶性能测试等方向做出了一系列开创性工作。
团队在汽车产业链的各个技术领域取得了优异的科技成果,出版汽车领域专著5部,授权国家发明专利100余项,曾获国家自然科学奖3次,教育部技术发明一等奖、汽车工业科学技术二等奖、国家企业创新一等奖等,具备丰富的科研和工程技术转化经验。
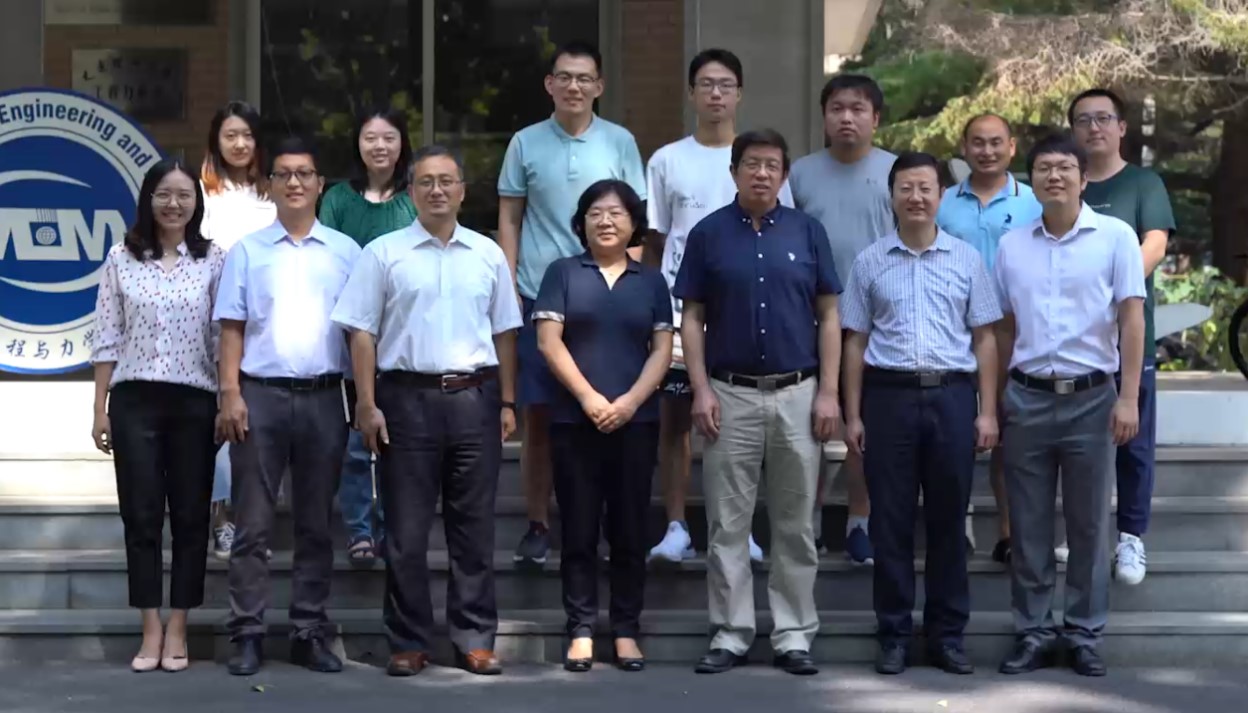
二、团队带头人
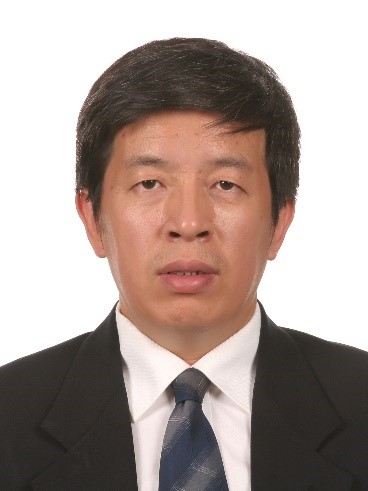
|
李刚教授:大连理工大学运载工程与力学学部部长,工业装备结构分析国家重点实验室主任、结构优化理论与应用国际联合研究中心主任,国防973计划首席科学家,国务院特殊津贴专家,辽宁省科技创新领军人才。长期从事重大装备与工程结构的性能设计研究,将结构优化、结构可靠性理论融入并形成自己的研究特色。先后主持国家自然科学基金重大研究计划集成项目课题、重点项目,以及973计划课题、863计划子课题、重大专项子课题等30余项。在本领域重要学术期刊发表160余篇,其中SCI检索80余篇,SCI他引1300余次;性能设计的代表性专著CNKI他引610余次,代表性论文单篇CNKI他引250余次,成为该研究领域的重要参文献。 |
三、团队研发方向
围绕宁波汽车产业链发展的关键技术需求,本项目拟建设1个汽车轻量化与智能化共性技术平台,重点展开4个专项任务的技术攻关,以形成以汽车先进设计技术、车用零部件复杂制造、新能源动力系统以及整车驾驶性能测试技术为代表的“闭环式”产业技术体系,为产业提供零部件与系统级的集成解决方案,可服务常规乘用车、新能源车、卡车、房车、智能车及特种改装车等整车与零部件产业的快速发展,促进产学研用的深度融合。
四、团队研究成果与应用领域
汽车轻量化设计与制造方面,建立了重大装备与工程结构的性能设计理论与方法,提出了车身结构概念设计技术,可大大缩短车身结构概念设计周期,并获得了中国汽车工业科学技术二等奖。
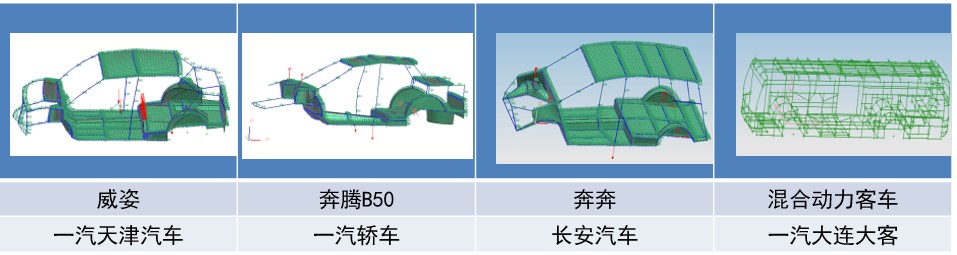
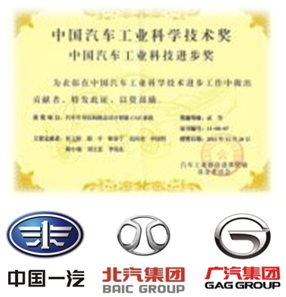
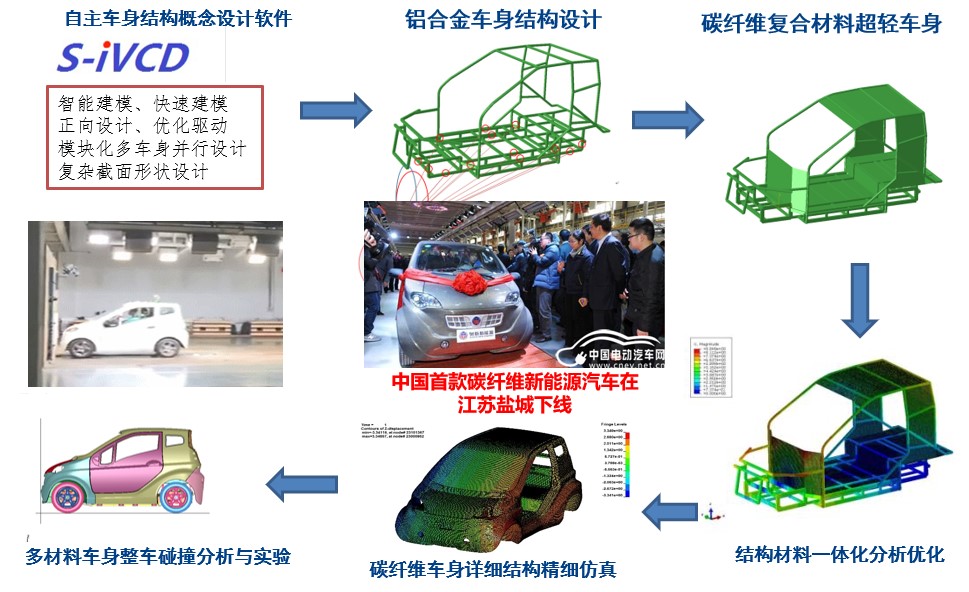
基于团队自主的车身结构设计技术和复合材料车身结构精细仿真技术,研发包括碳纤维增强复合材料上车身、防撞梁、电池箱等多种车身承载结构,实现了车身结构的大规模减重。
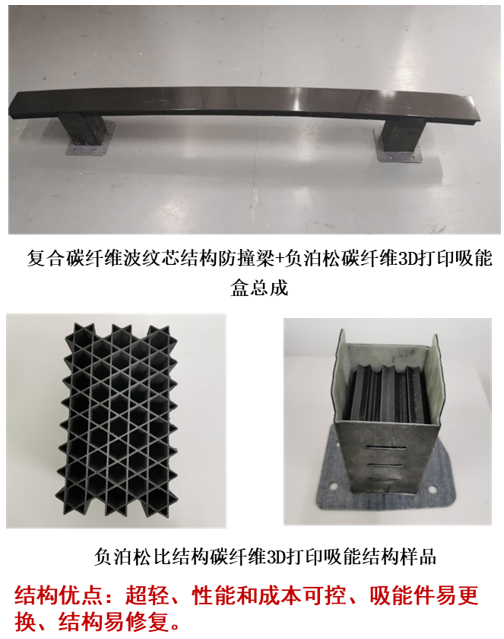
发了国内首台承载式车身底盘自动挡自行式房车。车辆结构采用先进复合材料技术,大幅降低了整车重量和能耗;结合多传感器融合技术、5G通讯和云端大数据分析技术,实现对房车健康和使用情况进行实时监测、手机远程控制。
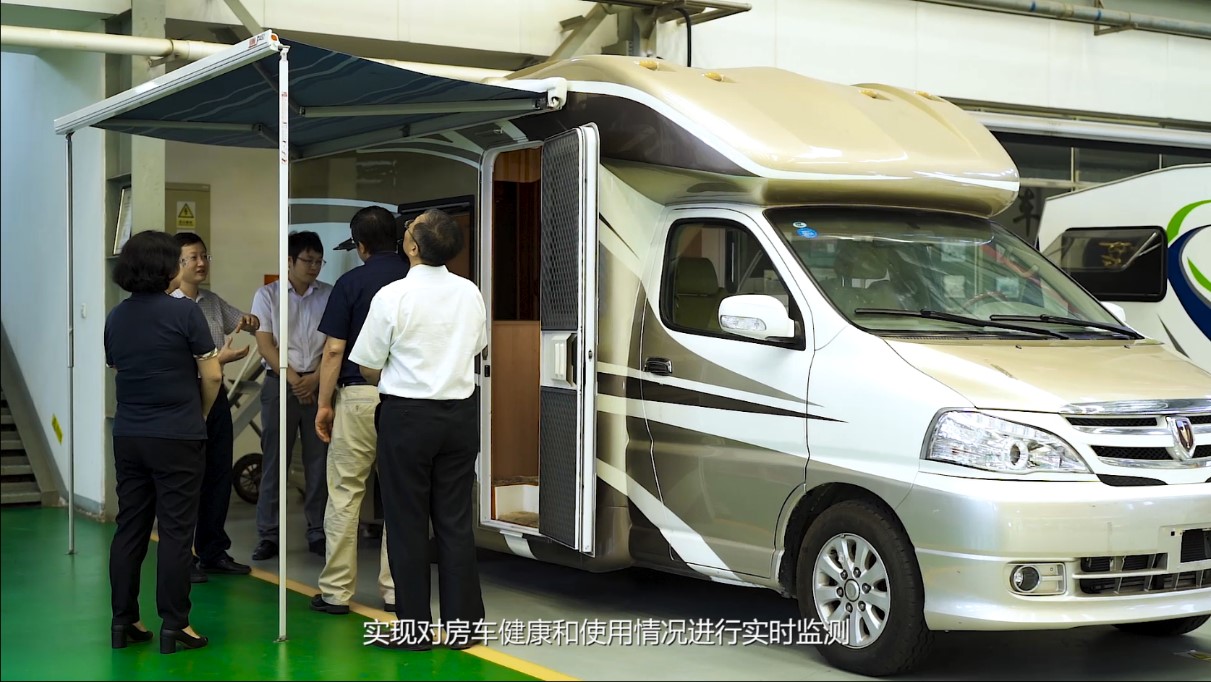
建立了人车协同系统,实现了驾驶舒适性的数字化判断;建立生理信号数据库,通过多模态生理信号复杂性的融合,建立生理检测模型;开发人工智能算法,实现车辆的高精度和高时序同步性控制。
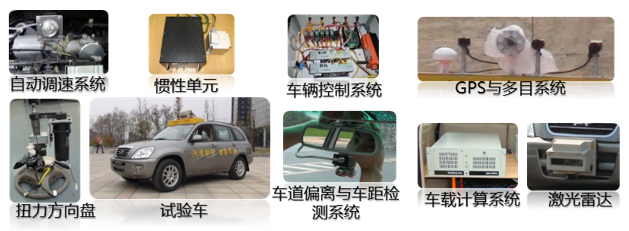
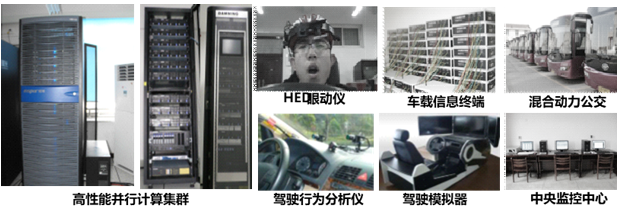
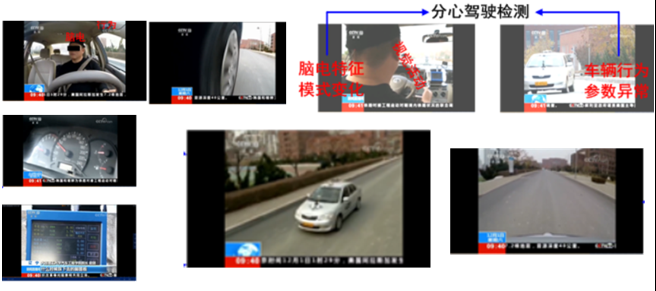
基于离线训练数据库,利用MATLAB完成灰狼优化MKRVM构建电池老化模型;
以测试数据库的电池充电数据通过LabVIEW文件I/O接口模拟实时电池硬件电路信号采集,逐行读取电池充电数据并存储为本地EXCEL文件,作为实时电池充电数据。当到达充电截止电流时,导入已保存的EXCEL文件,截取充电数据提取在线老化特征。
将训练完成的MKRVM优化模型嵌入到LabVIEW里,完成电池容量在线估算,并显示在BMS交互界面上。
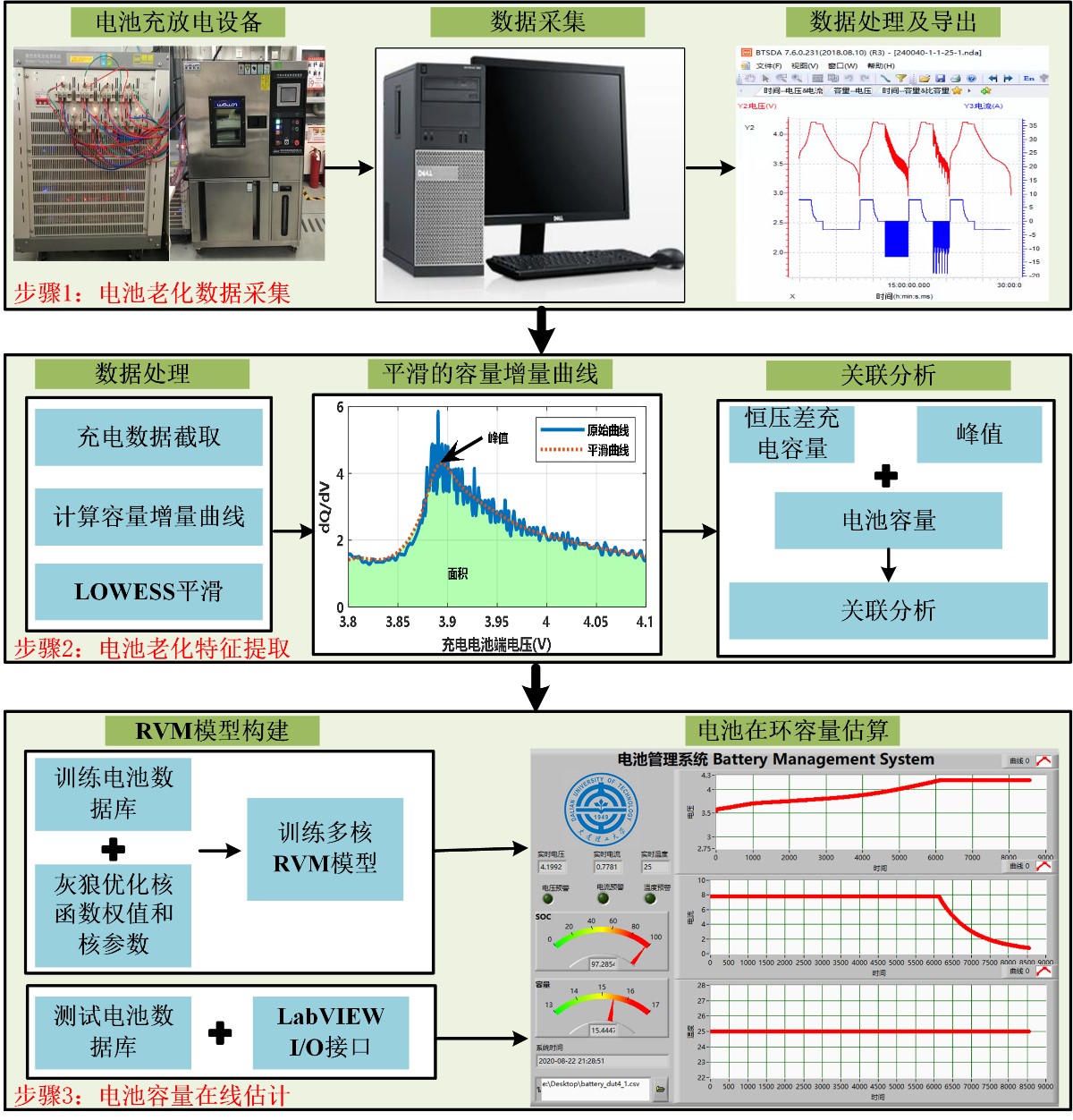
金属散热的车用三元锂电池动力电池组特色。
1.温度一致性好:任意两个单体电池温差可控制在5℃以内,有利于提升续航里程;
2.安全性好:具有一定吸能特性,但不会产生压溃,可有效防止外界冲击;
3.成本低:散热系统总成本占整个动力电池组的十分之一左右(量产会更低)。
研究满足法规要求机械安全性要求同时考虑分区板厚、材料匹配、形貌优化的动力电池包轻量化设计方法。
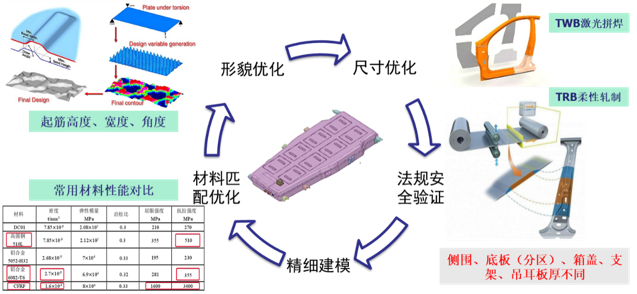
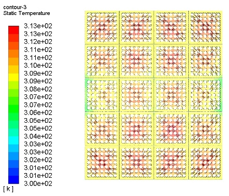
采用双向耦合模型和等效绕组的方法对电机进行温升分析,最大误差不超过6%。
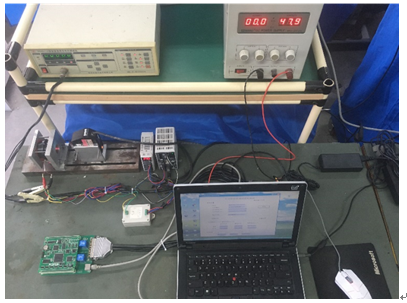
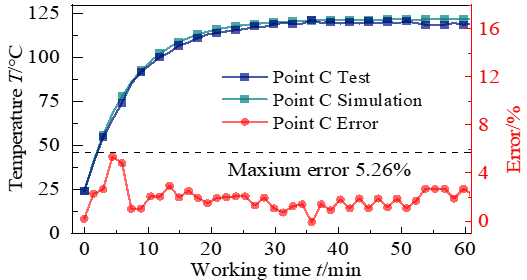
五、合作单位
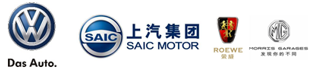
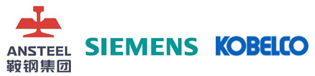